Perforated Parting Film Glue Suction G: A Comprehensive Guide
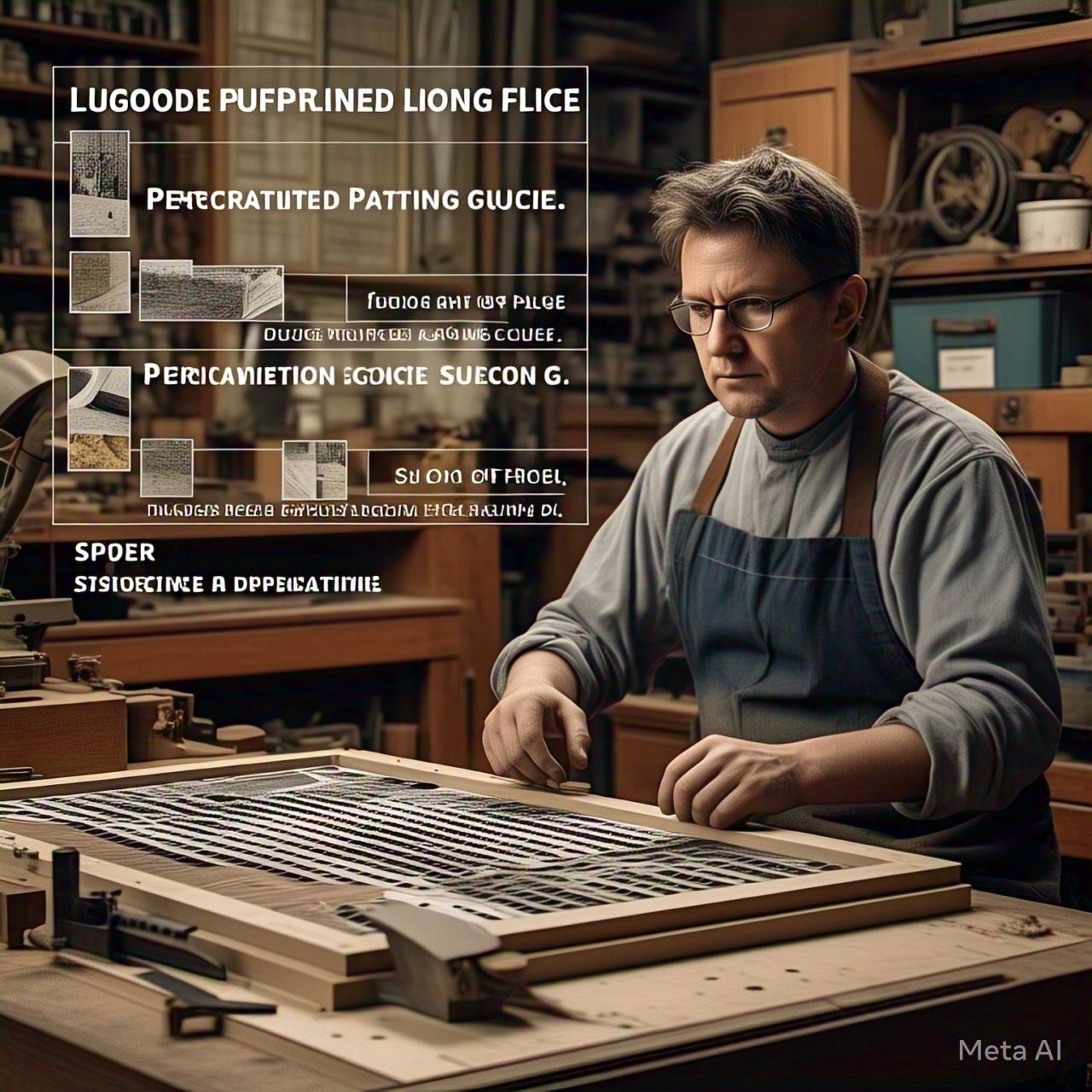
The perforated parting film glue suction g is an essential component in various industrial and manufacturing processes. It plays a crucial role in ensuring smooth mold separation, optimal adhesion control, and effective vacuum suction applications. Whether used in composite fabrication, aerospace engineering, or automotive manufacturing, this specialized material significantly improves efficiency and quality.
In this guide, we’ll explore the features, benefits, applications, and frequently asked questions about perforated parting film glue suction g to help you understand its importance in different industries.
What Is Perforated Parting Film Glue Suction G?
A perforated parting film is a thin, flexible material with precisely placed perforations that allow air or gases to pass through. When combined with glue suction, it provides controlled adhesion and easy mold release, making it ideal for vacuum molding, resin infusion, and composite fabrication processes.
Key Features
- Uniform Perforations: Ensures consistent air passage and controlled adhesion.
- High-Temperature Resistance: Suitable for industrial applications involving heat curing.
- Flexible and Durable: Maintains structural integrity during complex molding processes.
- Compatibility with Multiple Resins and Adhesives: Works effectively with epoxy, polyester, and other adhesive types.
- Improved Mold Release: Reduces defects and ensures a clean finish.
Applications of Perforated Parting Film Glue Suction G
The perforated parting film glue suction g is widely used in industries that require precise molding and adhesion control. Here are some of its most common applications:
1. Composite Manufacturing
Used in aerospace, automotive, and marine industries, this film helps create lightweight yet durable composite materials. It ensures smooth resin flow and prevents excess adhesive accumulation.
2. Vacuum Bagging and Resin Infusion
In vacuum-assisted resin transfer molding (VARTM), this film facilitates even resin distribution while allowing trapped air to escape, resulting in defect-free laminates.
3. Aerospace Industry
Manufacturers use perforated parting film glue suction g to create high-strength, lightweight aerospace components with minimal imperfections.
4. Automotive Sector
From body panels to structural components, this material is essential in automotive composite production, ensuring strong adhesion and seamless parting.
5. Industrial Tooling and Prototyping
Engineers and manufacturers rely on this film for prototype development, ensuring accurate mold replication and easy demolding.
Benefits of Using Perforated Parting Film Glue Suction G
Enhanced Mold Release Efficiency
The perforated structure prevents excess adhesive from accumulating, making it easier to remove molded components without damage.
Improved Adhesion Control
It ensures that glue or resin adheres only where necessary, reducing material waste and enhancing structural integrity.
Reduced Air Entrapment
The perforations allow trapped air to escape, eliminating voids and defects in composite materials.
Heat and Chemical Resistance
Designed for industrial applications, this film withstands high temperatures and exposure to various chemicals.
Cost-Effective Production
By improving mold separation and reducing defects, manufacturers save time and resources in post-processing and rework.
Choosing the Right Perforated Parting Film Glue Suction G
Selecting the best perforated parting film glue suction g depends on the specific requirements of your application. Here are some factors to consider:
1. Perforation Size and Pattern
Different industries require specific perforation sizes and patterns for optimal performance. Choose a film with suitable hole density to match your resin flow and air escape needs.
2. Thickness and Material Composition
Ensure the film is compatible with the materials you’re using. Some applications demand high-strength polymer films, while others require more flexible options.
3. Heat Resistance Level
Verify that the film can withstand your process’s curing temperature without deforming or losing functionality.
4. Adhesive Compatibility
Check whether the film works effectively with the adhesives and resins used in your manufacturing process.
How to Use Perforated Parting Film Glue Suction G Effectively
Preparing the Mold
Clean the mold surface to remove dust, debris, and contaminants that could affect adhesion and parting.
Applying the Film
Carefully place the perforated parting film glue suction g over the mold, ensuring even coverage. Secure it in place with tape or other suitable methods.
Vacuum Bagging (If Applicable)
If using a vacuum-assisted process, position the film correctly to facilitate optimal resin flow and air evacuation.
Curing and Demolding
Once the adhesive or resin cures, carefully remove the film to achieve a smooth, defect-free surface on the final product.
FAQs About Perforated Parting Film Glue Suction G
1. What industries commonly use perforated parting film glue suction g?
This material is widely used in aerospace, automotive, marine, industrial tooling, and composite manufacturing.
2. How does perforation size affect performance?
Smaller perforations allow controlled resin flow and air escape, while larger perforations may facilitate faster evacuation but could affect resin distribution.
3. Can I use perforated parting film glue suction g with all types of adhesives?
It is compatible with epoxy, polyester, and polyurethane adhesives, but you should verify its suitability for specific applications.
4. Does the film leave residue after removal?
High-quality perforated parting films are designed for clean removal without leaving residues, ensuring a smooth surface finish.
5. What temperature range can perforated parting films withstand?
Most industrial-grade films can handle temperatures up to 400°F (204°C) or more, depending on the material.
6. How do I store perforated parting film for long-term use?
Store in a cool, dry place, away from direct sunlight and moisture, to maintain its performance and longevity.
7. Can I customize perforation patterns for specific applications?
Yes, manufacturers offer custom perforation patterns and film thicknesses based on specific industry requirements.
8. What are the advantages of using glue suction in perforated parting film?
Glue suction improves adhesion control, prevents excessive resin buildup, and enhances mold release efficiency.
9. Where can I purchase perforated parting film glue suction g?
This material is available from industrial suppliers, composite material distributors, and specialized manufacturers.
10. How does this film improve vacuum bagging efficiency?
It allows trapped air to escape efficiently, ensuring even resin flow and defect-free composite production.
Conclusion
The perforated parting film glue suction g is an invaluable tool in modern manufacturing, providing enhanced adhesion control, improved mold release, and efficient vacuum-assisted resin infusion. Whether you’re working in aerospace, automotive, or composite fabrication, selecting the right film ensures high-quality results, reduced defects, and cost savings.
By understanding its features, applications, and best usage practices, industries can maximize efficiency and produce superior-quality products. If you’re looking for high-performance perforated parting films, be sure to explore trusted suppliers that offer customizable solutions to meet your specific needs.